FUTURE TRENDS IN CONVEYOR BELT TECHNOLOGY: WHAT TO EXPECT
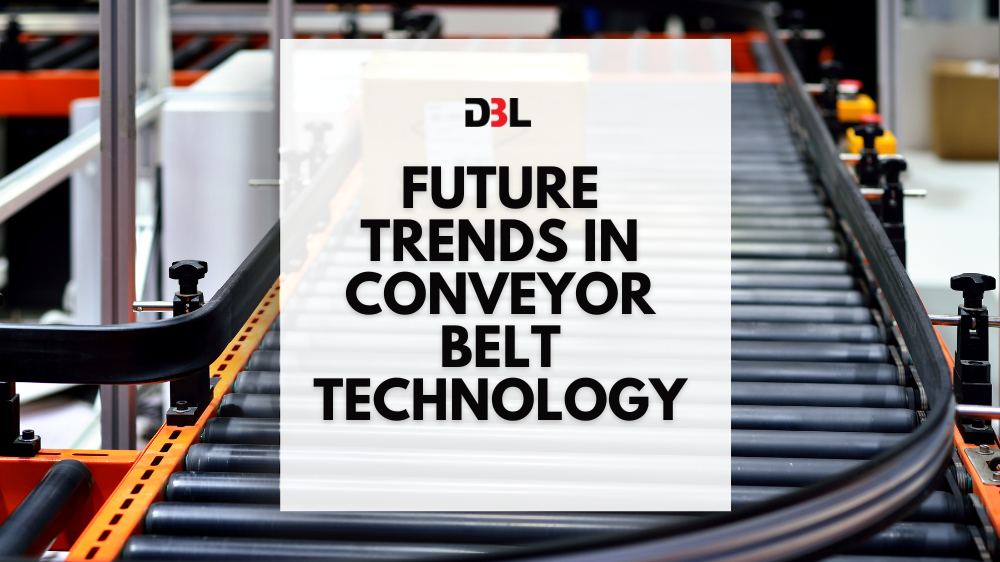
Conveyor belts have been important in the manufacturing and distributing industries for decades. They streamline processes, boost efficiency, and improve production. Their fundamental design allows them to move materials and products efficiently and speedily. However, as a result of the constant evolution of technology, there have been several innovations with regard to conveyor belt systems. These innovations give us a picture of what the future of conveyor belt technology looks like. They are as follows:
- Artificial Intelligence and Smart Automation.
A major innovation shaping the future of technology as a whole is artificial intelligence (AI) and smart automation. Conveyor belts are not left behind. AI algorithms can automate the whole conveyor belt process through the use of cameras and sensors to monitor the flow of products, detect irregularities, and make real-time adjustments to optimize efficiency. These algorithms can use data analysis to predict maintenance needs, causing a reduction in downtime and costly disruptions to operations. Machine learning capabilities would allow conveyor belts to adapt to changing production demands and increase output while reducing waste.
- Robotics
Related to artificial intelligence and smart automation, is the use of robotics. If you have watched any sci-fi film about the future, robots and artificial intelligence are at the forefront. This is not too far-fetched from reality, especially about the manufacturing industry. In the future, conveyor belt technology will be seamlessly integrated with robotic systems to create highly efficient production lines. Automated guided vehicles (AGVs) can interact with conveyor belts to transport goods between different stages of the production process, while robotic arms can perform intricate tasks such as sorting, packing, and palletizing. This combination of technologies will open the door to higher levels of productivity and accuracy in manufacturing.
- Flexible Design
Unlike the current traditional conveyor systems that are rigid, the future is in flexible and modular conveyor belt designs that can be adjusted easily to fit evolving production needs. Imagine conveyor belts that can be quickly expanded, contracted, or repositioned without extensive reengineering or downtime. This flexibility allows businesses to adapt rapidly to market fluctuations and scale their operations efficiently.
- Sustainable Technology
The future also emphasizes sustainable technology and industry practices due to increasing climate and environmental concerns. This is reflected in the conveyor belt industry with an increased focus on sustainable, eco-friendly materials and energy-efficient motors. Additionally, innovations such as regenerative braking systems can utilize energy during deceleration, reducing overall energy consumption and operational costs. Through these practices, conveyor belt systems could play an important role in building a greener future.
- Safety
Not only would conveyor belt systems be more sustainable in the future but they would also be safer. Safety is important in the manufacturing industry and this applies to conveyor belt technology. In the future, it is expected that there will be development and inclusion of advanced safety features aimed at protecting both workers and equipment. This includes technologies such as automatic emergency stop systems, obstacle detection sensors, and predictive analytics to identify potential hazards before they occur. By prioritizing safety, businesses can create a workplace environment that is not only more secure but also more productive.
In conclusion, the future of conveyor belt technology has a lot of potentials, driven by advancements in automation, AI, sustainability, and safety. By embracing innovation and investing in cutting-edge solutions, businesses can optimize their operations, increase productivity, and stay ahead in an ever-evolving marketplace.